Amazon will use computer vision to spot defects before dispatch
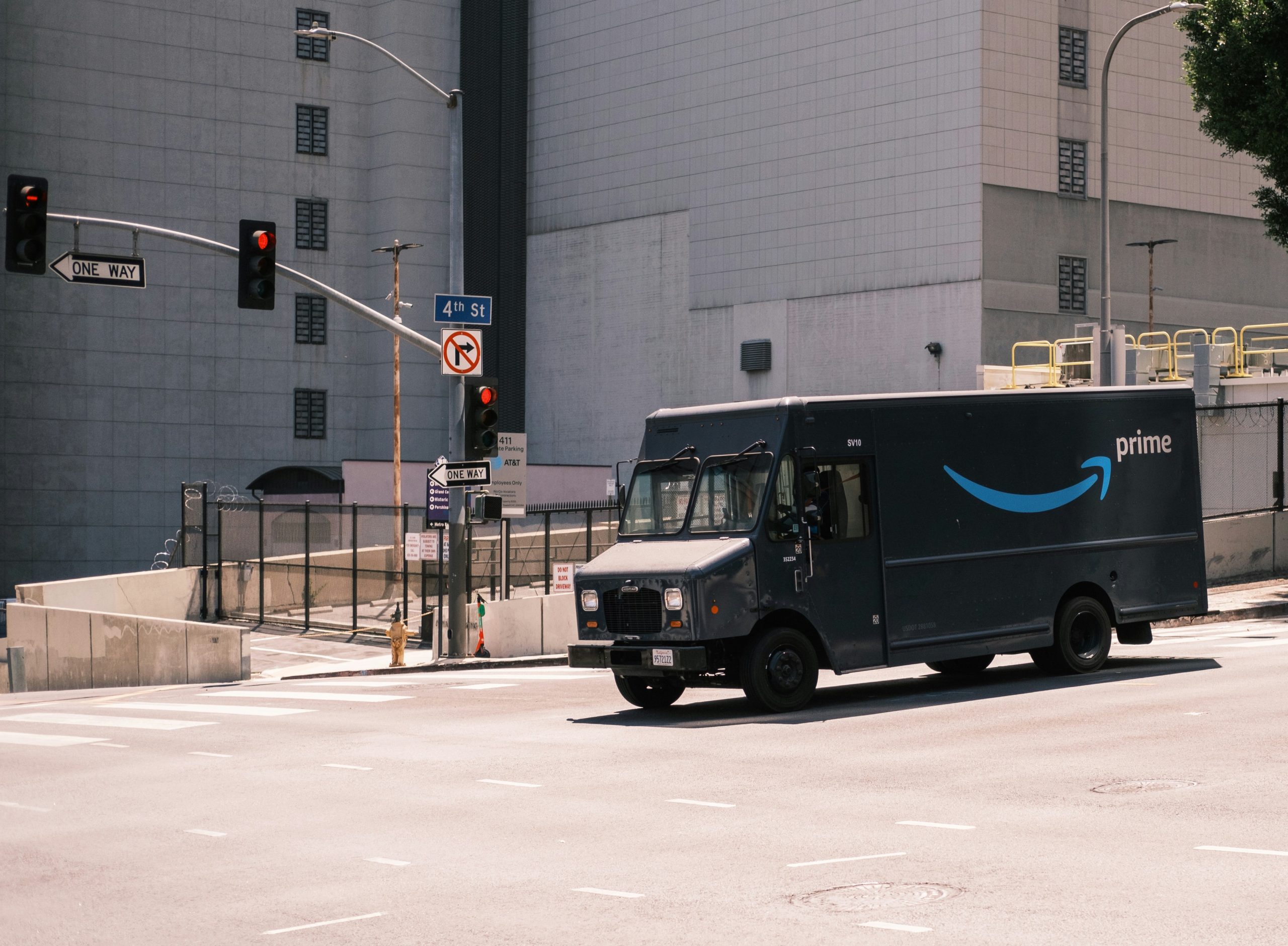
Amazon will harness computer vision and AI to ensure customers receive products in pristine condition and further its sustainability efforts. The initiative – dubbed “Project P.I.” (short for “private investigator”) – operates within Amazon fulfilment centres across North America, where it will scan millions of products daily for defects.
Project P.I. leverages generative AI and computer vision technologies to detect issues such as damaged products or incorrect colours and sizes before they reach customers. The AI model not only identifies defects but also helps uncover the root causes, enabling Amazon to implement preventative measures upstream. This system has proven highly effective in the sites where it has been deployed, accurately identifying product issues among the vast number of items processed each month.
Before any item is dispatched, it passes through an imaging tunnel where Project P.I. evaluates its condition. If a defect is detected, the item is isolated and further investigated to determine if similar products are affected.
Amazon associates review the flagged items and decide whether to resell them at a discount via Amazon’s Second Chance site, donate them, or find alternative uses. This technology aims to act as an extra pair of eyes, enhancing manual inspections at several North American fulfilment centres, with plans for expansion throughout 2024.
Dharmesh Mehta, Amazon’s VP of Worldwide Selling Partner Services, said: “We want to get the experience right for customers every time they shop in our store.
“By leveraging AI and product imaging within our operations facilities, we are able to efficiently detect potentially damaged products and address more of those issues before they ever reach a customer, which is a win for the customer, our selling partners, and the environment.”
Project P.I. also plays a crucial role in Amazon’s sustainability initiatives. By preventing damaged or defective items from reaching customers, the system helps reduce unwanted returns, wasted packaging, and unnecessary carbon emissions from additional transportation.
Kara Hurst, Amazon’s VP of Worldwide Sustainability, commented: “AI is helping Amazon ensure that we’re not just delighting customers with high-quality items, but we’re extending that customer obsession to our sustainability work by preventing less-than-perfect items from leaving our facilities, and helping us avoid unnecessary carbon emissions due to transportation, packaging, and other steps in the returns process.”
In parallel, Amazon is utilising a generative AI system equipped with a Multi-Modal LLM (MLLM) to investigate the root causes of negative customer experiences.
When defects reported by customers slip through initial checks, this system reviews customer feedback and analyses images from fulfilment centres to understand what went wrong. For example, if a customer receives the wrong size of a product, the system examines the product labels in fulfilment centre images to pinpoint the error.
This technology is also beneficial for Amazon’s selling partners, especially the small and medium-sized businesses that make up over 60% of Amazon’s sales. By making defect data more accessible, Amazon helps these sellers rectify issues quickly and reduce future errors.
(Photo by Andrew Stickelman)
See also: X now permits AI-generated adult content
Want to learn more about AI and big data from industry leaders? Check out AI & Big Data Expo taking place in Amsterdam, California, and London. The comprehensive event is co-located with other leading events including Intelligent Automation Conference, BlockX, Digital Transformation Week, and Cyber Security & Cloud Expo.
Explore other upcoming enterprise technology events and webinars powered by TechForge here.